Level measurement can be a critical operational parameter in industries ranging from oil and gas to water treatment. Among the various available technologies , pressure and differential pressure (DP) transmitters are widely used as fluid level monitoring devices. At its core, pressure-based level measurement established on the principle of hydrostatic pressure, the force exerted by a fluid at rest due to gravity. The pressure at any point in a liquid column is proportional to the height above that point, its density, and gravitational acceleration. The relationship is expressed by the formula:
P = ρ × g × h
Where:
P = Hydrostatic pressure
ρ = Fluid density
g = Gravitational acceleration
h = Height of the fluid column
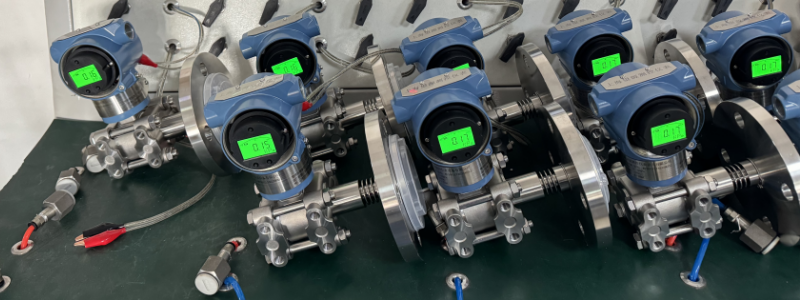
A pressure sensor positioned at the bottom of a tank can measure this pressure, then calculate liquid level and converts it into an electrical signal through circuit as long as the medium density is known.
Both Pressure and Differential Pressure Transmitters can be used for level measurement, but their applications differ based on working condition:
Pressure Transmitter
Measurement: The pressure relative to atmospheric pressure.
Scenario of use: Ideal for open tanks or channels where the liquid surface is exposed to the atmosphere. For example, in a reservoir, the transmitter’s output correlates linearly with water level.
Installation: Mounted at the tank’s base or submerged into fluid bottom.
Differential Pressure (DP) Transmitter
Measurement: The difference between two pressures: the hydrostatic pressure at the tank’s bottom and pressure above fluid surface.
Scenario of Use: Essential for closed/pressurized tanks where internal pressure (from gases, vapors, or vacuum) affects the measurement. DP measurement is able to compensate for the distortion and ensure accurate level data.
Installation: High-pressure side connects to the tank’s base while low-pressure side connects to the tank’s top.
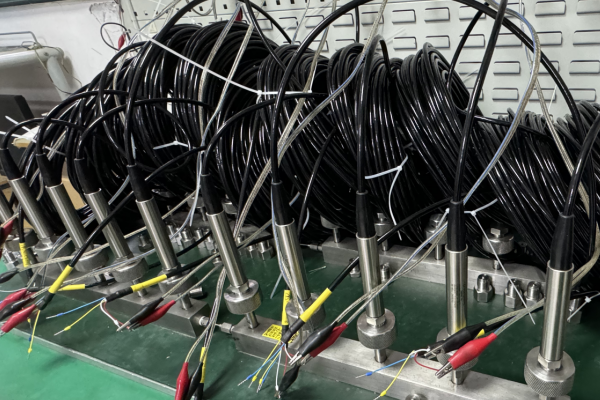
Key setup on pressure-based level measurement
Mounting Practice: Transmitters should be installed at the expected lowest liquid level to avoid dry measurement. Vessel structure and condition ought to ensure that submersible sensors can continuously immersed at the bottom. Impulse line tubing for DP transmitter must be free of blockages, leaks and gas bubbles.
Environmental and Medium Condition: Remote capillary connection can be applied to isolate sensors from heat to prevent electronic damage from extreme fluid temperature. Process connection with diaphragm seals or corrosion-resistant materials can protect sensor from aggressive fluid. Transmitter pressure rating should exceed maximum operating pressure including surge scenarios.
Advanced Feature and Integration: Modern technology can be introduced to enhance instrument reliability. Smart communications enable smooth integration with control systems and real-time diagnostics alerting fault or blockage. Multi-variable transmitters that measure level and temperature simultaneously could simplify installation and reduce cost.
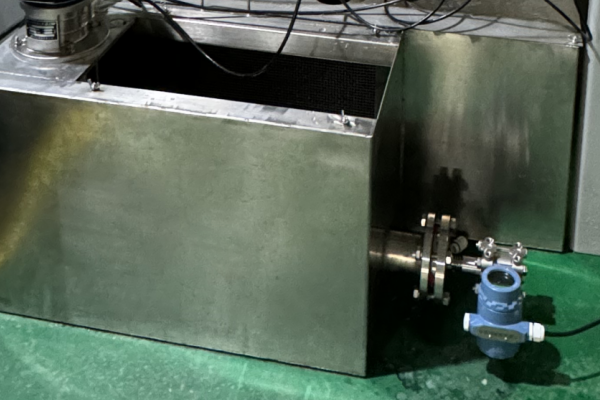
Pressure and differential pressure transmitters are versatile tools for level measurement, offering cost-effectiveness and adaptability across industries. Shanghai Wangyuan is an experienced manufacturer engaged in instrumentation industry. we would be delighted to hear from you, if you're in need of level monitoring solutions.
Post time: Feb-11-2025